-
Worldwide explosion protection!
Compliant with the most important directives and standards on an international level.
-
Wide-ranging and powerful performance
In environments with explosive air/gas mixtures or air/dust mixtures.
-
Precision, dynamics, and power
No problem, even in a potentially explosive environment.
-
Power, robustness, and safety
for tailor-made application solutions in potentially explosive areas.
Explosion protection: Directives and standards
Explosion-protected products available worldwide
Do you need to install explosion-protected products or is your system located in a potentially explosive atmosphere? Our products comply with the most important directives and standards worldwide.
Special measures need to be taken when using systems and machinery in areas with potentially explosive air/gas or air/dust mixtures. Corresponding standards and regulations govern the options for using equipment within established hazard zones.
The complex, internationally applicable requirements for using gearmotors, motors, or drive electronics in applications in potentially explosive atmospheres are set out in the most important directives and standards for the global market:
- ATEX: European Union and countries that recognize ATEX
- IECEx: Countries that recognize IECEx
- HazLoc-NA®: USA and Canada
- CCCEx: People’s Republic of China
- KOSHA: South Korea
- INMETRO: Brazil
- EACEx: Eurasian Customs Union
- UA.TR: Ukraine
- PESO: India (CCoE)
- UKEX: United Kingdom (UKCA)
Our gearmotors meet the defined requirements for equipment used in potentially explosive atmospheres. Unlike the internationally recognized IECEx rules or the North American regulations (HazLoc-NA®: SEW‑EURODRIVE brand name), EU Directive 2014/34/EU (ATEX) also includes non-electrical equipment in explosion protection. We will help you choose the right equipment features – an inquiry form can be downloaded here:
Your benefits
-
Safe use
Thanks to compliance with worldwide directives and standards for explosion-protected products. -
Outstanding versatility
Because our modular system offers numerous explosion-protected motors, gear units, and gearmotors. -
Worldwide availability
Because our explosion-protected products comply with ATEX, IECEx and/or HazLoc-NA®. -
Certified quality
Thanks to involvement in the creation of standards, continuous quality control, and innovative research and development.
But which standards and directives do you need to comply with when your system is being used worldwide?
All the details, the exact correlations worldwide, and an overview of the zones and assignment to equipment categories or EPL (Equipment Protection Levels) are shown here. And we have also compiled all the information related to SEW-EURODRIVE products that comply with these international guidelines and standards.
Country regulations
This map gives you a quick overview of which directives and standards apply in the respective country.
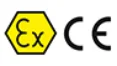
In the European Union, electrical and mechanical products must meet Directive 2014/34/EU and harmonized standards such as the EN 60079 series of standards. Category 2 equipment must be certified.

Motors for United Kingdom must be designed according to the "Equipment and Protective Systems Intended for Use in Potentially Explosive Atmospheres Regulations 2016".
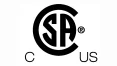
In the USA and Canada, electrical products must be certified according to NEC500 or C22.1 and are distinguished as Division 1 and Division 2, as well as Class I for gas and Class II for dust.
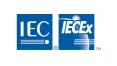
In New Zealand, the IECEx certification is accepted without additional certification or marking.
In South Africa, products in potentially explosive atmospheres must meet the requirements for SANS10108 and SANS ARP 0108 and have an IA certificate according to the Occupational Health and Safety Act 1993 (Act no. 85 of 1993).
SEW-EURODRIVE has not certified any products for this market.
In Japan, electrical equipment must be certified by certification companies that are based in and authorized in Japan.
SEW-EURODRIVE has not certified any products for this market.
The motors must meet the requirements of Indian standards. ATEX and IECEx certificates are accepted. In the gas sector, certification by the CCOE of the PESO is often required.
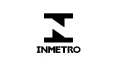
In Brazil, electrical equipment must meet INMETRO Regulation no. 179. The "INMETRO certification" is issued by the National Institute of Metrology, Quality, and Technology and marked accordingly.
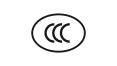
In the People’s Republic of China, electrical products must be certified according to the CNCA-C23-01:2019 implementation rules and Chinese standards.
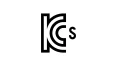
In the Republic of Korea (usually referred to as South Korea), products in potentially explosive atmospheres must be certified according to articles 34 and 35 of the "Occupational Safety & Health Act" and the local KOSHA (Korea Occupational Safety and Health Agency) standards.
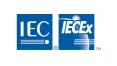
In Australia, the IECEx certification is accepted without additional certification or marking.
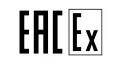
In the states of the Eurasian Customs Union, electrical and mechanical products must meet the technical rule set "TR CU 012/2011 Safety of equipment for work in explosive environments" and be certified according to the same.
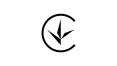
In Ukraine, electrical and mechanical products must meet the UA.TR technical rule set. Equipment and protective systems for potentially explosive atmospheres must be certified according to Regulation no. 1055 from December 2016.
Rule sets in detail
-
Europe (ATEX and others)
-
The IECEx certification agreement
-
HazLoc-NA® certification
For designated use in potentially explosive atmospheres in the European Union, the equipment and protective systems are described in Directive 2014/34/EU for the harmonization of the legislation of member states. The directive, also known as the ATEX directive, is primarily geared towards manufacturers and/or distributors of products that will be used in potentially explosive atmospheres.
This directive applies to gearmotors and motors, and has been in full legal force since April 20, 2016. Other European countries, such as Switzerland and Turkey, have also adopted this regulation.
There are no fundamental changes or new requirements for design-based explosion protection. The terminology contains significant new features compared to Directive 94/9/EC. The EC type examination is now known as the EU type examination, and the EC declaration of conformity has become the EU declaration of conformity. Existing EC type examination certificates will remain valid.
Directive 1999/92/EC primarily targets employers and system operators. It stipulates minimum regulations for safety requirements intended to prevent explosion-related accidents. In Germany, for example, this directive has been incorporated into national law with the Ordinance on Industrial Safety and Health (BetrSichV).
-
Product marking
-
Eurasian Customs Union - Russia, Belarus, Kazakhstan, Armenia
-
Ukraine
-
United Kingdom
- Manufacturer's name and address
- CE marking
- Designation of the series and type
- The serial number, if applicable
- The year of manufacture
- The special "Ex" marking for explosion prevention combined with an indication of the category
- For equipment group II, the letter "G" (for areas with potentially explosive gas, vapor, or mist/air mixtures)
- and/or the letter "D" (for areas in which dust could produce potentially explosive atmospheres)
The Eurasian Customs Union has adopted a number of European directives, with some modifications.
In the field of explosion protection, TR CU 012/2011, which is based on EU Directive 94/9/EC, has replaced the GOST regulations.
For products in potentially explosive atmospheres, the EAC marking (Eurasian conformity) alone, as found on standard motors for example, is not sufficient. The products must be certified according to the technical regulation "ТR СU 012/2011: Safety of equipment for work in explosive environments" and also receive an EX marking in addition to the EAC label.
The EACEx certification was created on the basis of the ATEX certification.
SEW-EURODRIVE asynchronous motors and asynchronous gearmotors are to be shipped with both labels.
The ATEX markings remain unchanged and the motor or gearmotor receives a second nameplate with the EACEx specifications. The second nameplate is always attached to the motor.
Stand-alone gear units are not to be shipped with both labels. The main nameplate is to be modified to fulfill all requirements of technical regulation ТR СU 012/2011.
Additional marking:
- EAC mark
- Ex marking
- Certification authority
- Certificate number
- EACEx marking for gas
- EACEx marking for dust
- Warning
Specifications are written in Cyrillic.
The Ukraine has also adopted some of the European directives, with modifications.
In the field of explosion protection, Regulation no. 1055 from December 2016 laid down technical standards for equipment and protective systems to be used in potentially explosive atmospheres.
Product marking
Motors for the Ukrainian market are certified according to the "Ukrainian Technical Regulations" (UA.TR) and are marked accordingly.
Motors for United Kingdom are designed according to the "Equipment and Protective Systems Intended for Use in Potentially Explosive Atmospheres Regulations 2016".
Product marking
For motors, there is the UK declaration of conformity and for category 2 motors, there is the "UK Type Examination Certification".
They are marked analogously to the European rules but with the UKCA marking.
When it comes to product labeling, the countries of England, Scotland and Wales are classed as the UK. Due to the Northern Ireland Protocol, the CE marking will continue to be used for Northern Ireland.
Worldwide platform for mutual recognition of certifications
The IECEx certification agreement serves as a worldwide platform for the mutual recognition of test results for obtaining certification or approval for explosion-protected electrical equipment. The basis is formed by the
- "IECEx 01 IEC Scheme for the Certification to Standards for Electrical Equipment for Explosive Atmospheres (IECEx Scheme) – Basic Rules" and
- "IECEx 02 IEC Scheme for the Certification to Standards for Electrical Equipment for Explosive Atmospheres (IECEx Scheme) – Rules of Procedure".
These two documents and other IECEx work documents are available free of charge in the IEC online shop at www.iecex.com.
Objectives of the IECEx agreement
The agreement serves to promote international trade with explosion-protected electrical equipment by eliminating double tests and certifications, which were required so far. The fundamental purpose of the agreement is to verify compliance with the IEC standards for electrical equipment in potentially explosive atmospheres in an internationally recognized form. It must be ensured that these standards are applied by test laboratories (ExTL, Ex-Testing Laboratories) and certification bodies (ExCB, Ex-Certification Bodies) so that assessment of a product's compliance with the standards provides the same results in every country.
Products from SEW-EURODRIVE are certified by the PTB as ExTL and ExCB according to IECEx and are available in the equipment protection levels (EPL) .b and c.
-
Product marking
-
Standards
-
Australia and New Zealand
-
South Korea
-
Brazil
-
India
-
People’s Republic of China
Basic marking according to IECEx
- IECEx mark of conformity for motors of the EDR.. series with IECEx marking license no. (PTB 001)
- Name and address of the manufacturer
- Manufacturer's type designation
- Serial number
- The name or ID of the authority that issues the certificate, and the certificate ID in the following form: the last two numbers of the year it was issued, followed by a period, followed by a unique four-digit series of characters for the certificate in that year (e.g. IECEx PTB 11.0041/01)
- The relevant Ex marking for potentially explosive gas atmospheres or for potentially explosive dust atmospheres
- All additional information for the relevant protection types
The most important standards for explosion protection are the standards of the IEC-60079 series:
- IEC 60079-0, Explosive atmospheres – Part 0: Equipment – General Requirements
- IEC 60079-1, Explosive atmospheres – Part 1: Equipment protection by flameproof enclosure "d”
- IEC 60079-7, Explosive atmospheres – Part 7: Equipment protection by increased safety "e"
- IEC 60079-10, Explosive atmospheres – Part 10-1: Classification of areas – Explosive gas atmospheres
- IEC 60079-10-2, Explosive atmospheres – Part 10-2: Classification of areas – Explosive dust atmospheres
- IEC 60079-11, Explosive atmospheres – Part 11: Equipment protection by intrinsic safety "i"
- IEC 60079-14, Explosive atmospheres – Part 14: Project planning, selection and setup of electrical machinery
- IEC 60079-15, Explosive atmospheres – Part 15: Equipment protection by protection type "n”
- IEC 60079-17, Explosive atmospheres – Part 17: Testing and maintenance of electrical machinery
- IEC 60079-19, Explosive atmospheres – Part 19: Equipment repair, overhaul and reclamation
- IEC 60079-31, Explosive atmospheres – Part 31: Equipment dust ignition protection by enclosure "t"
along with
- IEC 60079-2 Explosive atmospheres – Part 2: Equipment protection by pressurized enclosure "p"
- IEC 60079-5 Explosive atmospheres – Part 5: Equipment protection by sand filling "q"
- IEC 60079-6: Explosive atmospheres – Part 6: Equipment protection by oil immersion "o"
- IEC 60079-13 Explosive atmospheres – Part 13: Equipment protection by pressurized rooms
- IEC 60079-18 Explosive atmospheres – Part 18: Equipment protection by encapsulation "m"
Product marking
Australia and New Zealand recognize the IECEx certification directly. Furthermore, the motors must meet the efficiency requirements according to GEMS (Greenhouse and Energy Minimum Standard) Act 2012 and GEMS Determination 2019. The motors of the EDR.. series meet all these requirements and are registered according to GEMS.
No additional country-specific markings are required in either country.
As of October 01, 2018, explosion-protected motors with 0.75 kW and more must also correspond to the minimum efficiency level IE3. The EDRN.. motors meet these requirements and are equipped with the KEL (Korean Energy Label) according to the Korean efficiency levels.
In South Korea, products in potentially explosive atmospheres must be certified according to articles 34 and 35 of the Occupational Safety & Health Act from the KOSHA (Korea occupational Safety and Health Agency).
The Republic of Korea has joined the IECEx agreement. Test reports required for the IECEx certification of the EDR.. motors are approved by KOSHA. However, individual certificates for the respective motors are issued. South Korean regulations are guided by the series of standards IEC 60079 for gas and IEC 61241-1 for dust. Potentially explosive atmospheres are classified according to KS C IEC 60079-10. Equipment is selected according to KS C IEC 60079-14.
Certified motors are marked with the KCs logo and the certification number. In addition, the marking according to the Korean standards is specified. The texts with the certification number and the marking have Korean characters. The data is supplemented with KOSHA as approval authority.
The standards currently valid in South Korea do not match the current editions of the IEC standards. For this reason, certifications from KOSHA include the explosion protection markings valid for Korea. EDRN.. motors have been developed and manufactured according to the latest IEC standards. Therefore, the motors are marked with the IEC identification. South Korean authorities recognize these identifications. In addition, the identifications according to the Korean standard are marked on the nameplate.
The table shows a comparison of the marking of explosion protection
Close table
EDRN.. | Identification according to Korean standards | Identification according to IEC |
---|---|---|
2G-b | Ex e IIC T3 | Ex eb IIC T3 Gb |
3G-c | Ex nA IIC T3 | Ex ec IIC T3 Gc |
2D-b | Ex tD A21 IP65 T120 °C | Ex tb IIIC T120 °C Db |
3D-c | Ex tD A22 IP54 T120 °C | Ex tc IIIB T120 °C Dc |
Ex tD A22 IP65 T120 °C | Ex tc IIIC T120 °C Dc |
We have stored a table for you here.
The motors have been certified by the Korean KOSHA according to the following standards.
Close table
Medium | Explosion protection | General standards | Specific standards |
---|---|---|---|
Gas | Increased safety "e" | KS C IEC 60079-0 | KS C IEC 60079-7 |
Degree of protection "n" | KS C IEC 60079-15 | ||
Dust | Protection by enclosure "tD" | KS C IEC 61241-0 | KS C IEC 61241-1 |
We have stored a table for you here.
Product marking
Additional marking:
- KCs - marking
- Certification authority
- Certificate number
- Korean explosion protection marking
Additional marking:
- KCs - marking
- Certification authority
- Certificate number
- Korean explosion protection marking
Brazilian regulations require certificates of conformity (CoCs) issued by the National Institute of Metrology, Quality and Technology (INMETRO). The IECEx CoC is not valid in Brazil, even though ExTRs are recognized and form part of the INMETRO CoC.
Areas exposed to explosion hazards are defined for the Brazilian market in the regulations Nº 179, from May 2010, and Nº 89, from February 2012.
EDR.. motors are certified by the DNV certification authority based on the IECEx certification according to the requirements of the Brazilian authority INMETRO. This also includes certification of the production sites.
Additional marking:
- Specification of the Brazilian motor standard
- Type of starting behavior
- Relation between starting current and rated current
- Motor type: Induction motor with squirrel-cage rotor
- INMETRO logo, ExCB logo (DNV) and number
- Explosion certificate numbers
- Energy efficiency class
- Wiring diagrams
In India, there are two important standards for determining and selecting electrical equipment:
- IS 5571: Guide for Selection and Installation of Electrical Equipment for Hazardous Areas (other than mines). This standard is based on IEC 60079‑14.
- IS 5572-2009: Classification of hazardous areas (other than mines) having flammable gases and vapors for electrical installation. This standard quotes IEC 60079‑10.
Operating resources in protection type n (non-sparking) and e (increased safety) are permitted in zone 2 only. Motors in flameproof enclosure protection type "d" must be used for zone 1.
For operating resources in potentially explosive areas with gas atmosphere, the approval by the Chief Controller of Explosives (CCE or CCoE) is often prescribed.
Approval from the Chief Controller of Explosives (CCoE) is obligatory for all electrical equipment installed in potentially explosive atmospheres. Rule 106 of the Petroleum Rules 2002 specifies that all electrical equipment used in potentially explosive atmospheres require CCoE approval. Approval for such equipment is therefore only limited to areas covered by the "Petroleum and Explosives Safety Organization" (PESO).
As of January 1, 2018, motors must meet the requirements of Indian standard IS12615 "Line Operated Three Phase a.c. Motors (IE CODE) – Efficiency Classes and Performance Specification". Therefore, motors must at least meet the requirements of energy efficiency class IE2.
However, motors designed for use in explosion-protected areas are not subject to the requirements of IS12615.
Additional marking:
Motors that are certified by CCoE are marked with:
- Manufacturer's name
- Manufacturer's type designation
- Number and date of the certificate according to approval
- Equipment reference number according to approval
- Ex degree of protection
In accordance with the Chinese energy efficiency regulation GB18613, explosion-protected motors must also meet the requirements of at least Chinese Grade 3. The motors are marked with the CEL (Chinese Energy Label).
Starting on June 1, 2021, the new GB 18613-2020 prescribes Grade 3, equivalent to energy efficiency class IE3 for 0.12 kW and higher. According to the CEL007/2021 implementation ordinance, only motors from 0.75 kW to 375 kW require marking.
As of October 1, 2020, products that are intended for use in potentially explosive atmospheres must be certified and meet the requirements of the "China Compulsory Product Certification CCC for Explosion-proof Electrical Products". Without this certification, they may not be delivered, sold, imported, or used in other business activities.
The CCC Certification is based on the CNCA-C23-01:2019 implementation rules and the Chinese standards. The term typically used is CCCEx.
EDRN.. motors from SEW-EURODRIVE have been developed and manufactured according to the latest IEC standards. Therefore, they bear the identifications according to IEC and IECEx.
The standards currently valid in the PR China currently do not match the editions of the international IEC standards. For this reason, certifications according to CCC include the explosion protection identifications valid for China.
In order to meet the requirements of Chinese standards and authorities, the motors will receive a new nameplate. In this case, this is the primary nameplate. In addition, the motor receives the associated IECEx plate.
This indicates that the motors are approved under both CCCEx and IECEx.
The table shows a comparison of the marking of explosion protection
Close table
EDRN.. | Identification according to Chinese standards | Identification according to IEC |
---|---|---|
2G-b | Ex e IIC T3 Gb | Ex eb IIC T3 Gb |
3G-c | Ex nA IIC T3 Gc | Ex ec IIC T3 Gc |
2D-b | Ex tD A21 IP65 T120 °C | Ex tb IIIC T120 °C Db |
3D-c | Ex tD A22 IP54 T120 °C | Ex tc IIIB T120 °C Dc |
Ex tD A22 IP65 T120 °C | Ex tc IIIC T120 °C Dc |
We have stored a table for you here.
The motors were certified by the Chinese NEPSI (National Supervision and Inspection Center for Explosion Protection and Safety of Instrumentation) according to the following standards.
Close table
Medium | Explosion protection | General standards | Specific standards |
---|---|---|---|
Gas | Increased safety "e" | GB3836.1 – 2010 | GB3836.3 - 2010 |
Degree of protection "n" | GB3836.8 - 2014 | ||
Dust | Protection by enclosure "tD" | GB12476.1 – 2013 | GB12476.5 – 2013 |
We have stored a table for you here.
Additional marking:
- CCC marking
- Certification authority
- Certificate number
- Chinese explosion protection marking
- Production facilities
- Manufacturer
Certified by CSA for the North American market
HazLoc-NA® (Hazardous Location Northern America) is a synonym for explosion protection in North America, like ATEX for Europe or IECEx for many other countries.
Unlike ATEX and IECEx where the areas in which a potentially explosive atmosphere may be present are divided into zones (0, 1, 2, 20, 21, 22), NEC500 and C22.1 make a distinction between division 1 and division 2 as well as between class I for gas and class II for dust.
Our products for the North American market for use in potentially explosive atmospheres in division 2 are certified by the CSA and bear the CSA logo.
This certification confirms that the motors and options were tested and that they met the applicable standards for safety and/or performance, including the relevant standards defined or managed by:
- The Canadian Standards Association (CSA),
- The American National Standards Institute (ANSI)
- Underwriters Laboratories (UL) and
- NFPA70 (the National Fire Protection Association)
.
-
Product marking
CSA marks are accepted by many manufacturers, retailers, regulators and inspectors in the electrical, gas, building and plumbing sectors throughout the USA and Canada.
Motors for explosive atmospheres must also meet efficiency requirements in the USA and Canada. This is indicated by the corresponding CSA logo for Canada and the marking according to CFR 431 for the USA.
Additional product marking
- CSA label
- Master Contract No. 170602
- Type designation
- Electrical rated values in volts, horsepower or kW, ampere, and rpm
- Serial number
- Hazardous Location Designation
- CLASS I, DIVISION 2, GROUPS A, B, C & D; Temperature Code T3C or T3
- CLASS II, DIVISION 2, GROUPS F & G; Temperature Code T4A or T3C
- Insulation class
- Power factor
- Degree of protection (totally enclosed, fan-cooled)
- Ambient temperature range
- Manufacturing location
- Electrical data of the brake (voltage, current)
Products in detail
-
Gear units and motors
-
Gearmotors
-
Industrial Gear Units
Explosion-protected gear units
- Standard gear units of the 7 and 9 series
- Servo gear units of the BS.F series and PS.F series
Explosion-protected motors
Explosion-protected gearmotors
In the European Union, mechanical equipment is also included in explosion protection. To our knowledge, there are no specific requirements for gear units as mechanical components anywhere in the world.
The gearmotors are fully compliant with European Directive 2014/34/EU. In our II2GD gas/dust designs and II3GD design, they offer you an optimum ratio between power and explosion protection.
In countries that do not have any special requirements, motors based on the IECEx or HazLoc-NA®approval can also be combined with standard gear units.
We recommend using gear units with explosion protection, since they are manufactured according to the IEC 80079-36 and 37 standards, which are also valid internationally, and are also marked as such.
Various combination options!
Take advantage of our modular system and combine an explosion-protected AC motor with an explosion-protected helical, parallel-shaft helical, helical-worm, helical-bevel, or SPIROPLAN®gear unit of your choice. And in the case of applications in the servo area, we have the right explosion-protected servomotor together with an explosion-protected planetary or helical-bevel gear unit in our range.
Explosion-protected industrial gear units
Basic information regarding ATEX/IECEx explosion protection
-
Categories, protection level, and zones
-
Gas groups, dust groups and use of equipment
-
Ex markings for motors
-
Ex labeling for gear units
Directive 2014/34/EU defines only basic requirements. Product-specific requirements are defined in the various applicable standards. On an international level, IEC 60079-0 ("Explosive atmospheres - Equipment - General requirements") introduced the EPL (Equipment Protection Level). These equipment protection levels indicate the suitability of equipment for use in potentially explosive areas according to zone classifications.
With the revision of EN 60079-0 issued in 2010, the EPL were also adopted in European standards. Equipment must now be designed with explosion protection measures of varying degrees as appropriate to the relevant category or EPL protection level.
Classification of Zone – Category/EPL – Degree of Protection
Close table
Zone | Category | EPL | Degree of protection | Frequency/duration | Guaranteed protection | |
---|---|---|---|---|---|---|
0 20 |
1 | G D |
Ga Da |
Very high |
for long periods or frequently | With two independent preventive measures; two faults are allowed to occur independently of one another |
1 21 |
2 | G D |
Gb Db |
High | Occasionally in normal operation | One preventive measure; suitable for normal operation with the likeliness of frequent malfunctions, one fault is allowed to occur |
2 22 |
3 | G D |
Gc Dc |
Normal | Usually not or only for a short period, in normal operation | Suitable for normal operation |
We have stored a table for you here.
Equipment groups according to directive
Equipment group I: Applies to equipment used in below-ground mining operations and their above-ground systems that may be subject to hazards from firedamp and/or flammable dusts.
Equipment group II: Applies to equipment to be used in other areas that may be subject to hazards from a potentially explosive atmosphere.
The equipment groups according to ATEX should not be confused with the groups according to the standard.
The IEC 60079-0 standard defines the classification of the equipment
Group I: Equipment for operation in openings with a risk of firedamp;
Group II: divided into Groups IIA, IIB and IIC, equipment that is intended for operation in areas in which potentially explosive gas atmospheres are expected, with the exception of mine openings with a risk of firedamp;
Group III: divided into groups IIIA, IIIB and IIIC, equipment that is intended for operation in areas in which potentially explosive dust atmospheres are expected, with the exception of mine openings with a risk of firedamp.
The following table describes the categorization of explosion-protected operating resources in equipment group I and II, as well as the assignment of equipment category, zone and protection type.
Close table
Equipment group II Other areas with potentially explosive atmospheres due to gas or dust |
||||||
---|---|---|---|---|---|---|
Equipment category | 1 | 2 | 3 | |||
Potentially explosive atmospheres1) |
G | D | G | D | G | D |
Zone | 0 | 20 | 1 | 21 | 2 | 22 |
Protection type | ||||||
Motor | – | d (db), e (eb) | t (tb) | e (ec) | t (tc) | |
Brakemotor2) | – | d (db) | t (tb) | e (ec) | t (tc) | |
Gear Unit | – | h (c, k, ...) | h (c, k, ...) | h (c, k, ...) | h (c, k, ...) | |
|
We have stored a table for you here.
Note
All gear units and motors offered by SEW-EURODRIVE for potentially explosive atmospheres are equipment group II units. SEW-EURODRIVE does not supply any drives for use in equipment group I (mining).
Gas groups
Group II is reserved for equipment for areas with potential risk of gas explosions. Electrical and non-electrical equipment in equipment group II is additionally divided into explosion groups IIA, IIB, and IIC. The hazard increases from A to C.
Close table
Gas explosion group (IEC / EN 60079-0, -20) | ||||||
---|---|---|---|---|---|---|
Group II | Gases and vapors (excerpt) | |||||
IIA | Ammonia Methane Ethanol Propane |
Ethyl alcohol Cyclohexane n-butane |
Gasoline General jet fuel n-Hexane |
Acetaldehyde | ||
IIB | Acrylonitrile town gas |
Ethylene Ethylene oxide |
Ethyl glycol Hydrogen sulfide |
Ethyl ether | ||
IIC | Hydrogen | Ethyne (acetylene) |
Carbon disulfide | |||
Temperature classes | T1 max. 450 °C |
T2 max. 300 °C |
T3 max. 200 °C |
T4 max. 135 °C |
T51) max. 100 °C |
T61) max. 85 °C |
|
We have stored a table for you here.
Dust groups
Group III is reserved for equipment in explosive dust atmospheres and is divided into additional sub-groups:
- IIIA – Flammable lint
- IIIB – Non-conductive dusts
- IIIC – Conductive dusts
The table shows the required minimum degree of protection depending on the protection level and the dust group.
Close table
Protection level | Equipment in group | ||
---|---|---|---|
IIIC Conductive dusts |
IIIB Non-conductive dusts |
IIIA Flammable lint |
|
ta | IP6X1 | IP6X1 | IP6X1 |
tb | IP6X1 | IP6X1 | IP5X1 |
tc | IP6X1 | IP5X1 | IP5X1 |
|
We have stored a table for you here.
Equipment sold within the scope of European Directive 2014/34/EU must be labeled in accordance with Directive 2014/34/EU in addition to carrying the standard label (EN 60079-0 or IEC 60079-0).
Close table
Label according to | |
---|---|
Directive | Standard |
II2G | Ex eb IIC T3 Gb |
II3G | Ex ec IIC T3 Gc |
II2D | Ex tb IIIC T120 °C Db |
II3D | Ex tc IIIB T120 °C Dc |
II3D | Ex tc IIIC T120 °C Dc |
We have stored a table for you here.
We provide gearmotors and motors for use in potentially explosive atmospheres in accordance with the relevant EN and IEC regulations. This means that the drives can be used both in the European Union, and in countries that recognize IECEx. This also applies to options and accessories in an explosion-protected design.
Designation according to EU Directive
At least the following information must be attached visibly and permanently to each unit and protection system:
- Name, registered trade name, or registered trade brand, and manufacturer's address
- CE marking (see annex II to regulation (EC) no. 765/2008)
- Designation of the series and type
- If applicable, batch number or serial number
- Year of manufacture, hexagonal explosion protection mark, and the mark for equipment group and equipment category.
- For equipment group II, the letter G (for areas with potentially explosive gas, vapor or mist/air mixtures).
- The letter D (for areas in which dust/air mixtures could produce potentially explosive atmospheres).
In addition, all safety-relevant information must be attached to the equipment before operation.
Marking in accordance with directives and standards
The protection types are linked to equipment groups, categories, potentially explosive atmospheres, minimum degrees of protection and temperature classes, and are indicated on the nameplate according to EU Directive 2014/34/EU.
The identification according to the standard includes the following symbols:
- The Ex symbol, which indicates that the electrical equipment meets the requirements of one or more protection types.
- Symbol for the relevant protection type
- Symbol for the group plus information on gas or dust
- Temperature class for gas or maximum surface temperature for dust
- Equipment protection level (EPL)
The IECEx identification consists of the normative part.
Example 1:
Operating resources in protection type e for increased safety:
0102 II 2G Ex eb IIC T3 Gb
Example 2:
Operating resources in protection type t for dust explosion protection provided by the enclosure:
II 3D Ex tc IIIC T120 °C Dc
Close table
Example 1 | Example 2 | Meaning | |
---|---|---|---|
![]() |
Marking according to the EU Directive |
CE marking | |
0102 | Identification number of the notified body (here: PTB), only for category 2 | ||
![]() |
Explosion protection mark | ||
II | Equipment group | ||
2 | 3 | Equipment category | |
G | D | G for areas containing potentially explosive mixtures of gas, vapor, mist, and air. D for areas in which dust/air mixtures could produce potentially explosive atmospheres. |
|
Ex | Labeling to standard |
Symbol indicating that the equipment complies with one or more protection types | |
eb | tc | Information on the protection type/protection level eb: Increased safety tc: Protection by enclosure |
|
IIC | IIIC | IIC: Gas group IIIC: Dust group |
|
T3 | T120 °C | T3: Temperature class T120 °C: Maximum surface temperature in degrees Celsius |
|
Gb | Dc | Equipment protection level (EPL) |
We have stored a table for you here.
EN ISO 80079-36 and -37
The EN ISO 80079-36 and -37 standards specify the basic requirements for design, constructing, testing and labeling non-electrical equipment intended for use in potentially explosive atmospheres.
The EN ISO 80079-36/-37 standards were published in the official journal of the European Union in 2016 and replace the EN 13463-1/-5/-6/-8 standards. The transition period ended on October 31, 2019.
SEW‑EURODRIVE has applied the standards at an early stage to give our customers the opportunity to evaluate their entire systems according to the standards.
Labeling has changed significantly and has been adapted to the labeling system for electrical equipment.
The previous labeling with protection type "c" (protection by design safety) or "k" (protection by liquid immersion) has been dropped and replaced by the new letter "h".
Close table
Equipment category |
Explosive atmosphere | Old label according to EN 13463-1/-5/-8 | New label according to EN ISO 80079-36/-37 |
---|---|---|---|
2 | Gases/vapors | c, k T4/T120 °C | Ex h IIC T4 Gb |
2 | Dust/air mixtures | Ex h IIIC T120 °C Db | |
3 | Gases/vapors | c, k T4/T120 °C | Ex h IIC T4 Gc |
3 | Dust/air mixtures | Ex h IIIC T120 °C Dc |
We have stored a table for you here.
Equipment sold within the scope of European Directive 2014/34/EU must be labeled in accordance with Directive 2014/34/EU in addition to carrying the standard label.
Close table
Labeling according to directive ATEX 2014/34/EU | Labeling according to standard EN ISO 80076-36/-37 | |||||||
---|---|---|---|---|---|---|---|---|
(1) | (2) | (3) | (4) | (5) | (6) | (7) | (8) | (9) |
II | 2 | G | Ex | h | IIC | T4 | Gb | |
II | 2 | D | Ex | h | IIIC | T120 °C | Db | |
II | 3 | G | Ex | h | IIC | T4 | Gc | |
II | 3 | D | Ex | h | IIIC | T120 °C | Dc |
We have stored a table for you here.
Close table
Position | Identification | Symbol | Meaning |
---|---|---|---|
(1) | EX logo for equipment |
![]() |
Explosion protection mark |
(2) | Equipment group | II | Equipment outside of underground operations |
(3) | Equipment category | 2 or 3 | 2 – suitable for zones 1 or 21 3 – suitable for zones 2 or 22 |
(4) | Explosive atmosphere | G or D | G – suitable for gas, vapor, mist, etc. D – suitable for dust |
(5) | Ex marking | Ex | Ex marking according to EN ISO 80076-36/-37 |
(6) | Type of protection | h | Non-electrical equipment for use in explosive atmospheres |
(7) | Suitable atmosphere | IIC or IIIC | IIC – suitable for gas IIIC – suitable for conductive dust |
(8) | Permitted temperature | T4 or T120 °C |
T4 – Temperature class T120 °C – max. surface temperature |
(9) | Equipment protection level (EPL) | Gb, Db or Gc, Dc |
Gb, Db – "high" level of protection Gc, Dc – "advanced level of protection" |
We have stored a table for you here.
Example of a gearmotor nameplate
Example of a gear unit nameplate
Basic information regarding HazLoc-NA® explosion protection
-
Certification
-
Class Division
-
Groups, temperature classes, and degree of protection
-
Identification
In the USA and Canada, electrical equipment and operating resources in potentially explosive premises require a certification. An exception are electrical operating resources that cannot ignite the surrounding potentially explosive atmosphere due to their construction and properties.
The responsible authority has to decide if an approval is required. In the USA and Canada, equipment designed and manufactured for use in potentially explosive areas is tested and approved by nationally renowned inspection authorities. In the USA, responsible authorities are for example Underwriters Laboratories (UL) or Factory Mutual (FM), and, in Canada, the Canadian Standards Association (CSA).
Division
Potentially explosive areas are divided in division 1 and division 2 according to the frequency and duration that these substances occur in. The definition is based on NEC 500.5 and/or CSA 22.1, and is specified according to the classes.
Division 1
Areas with inflammable concentrations of inflammable or combustible substances that have contact to the motor.
Division 2
Areas with inflammable concentrations of inflammable or combustible substances that are stored in closed systems or containers and usually have no contact to the motor.
Class
The class defines a general limit of the physical properties of the hazardous substances.
Class I
Gases, vapors, and liquids that can be present in sufficient quantities to be explosive or ignitable.
Class II
Dust or combustible dust that can be present in sufficient quantities to create potentially explosive mixtures or electrically conductive dust.
Groups
Close table
Assignment of groups A – D in class I | Assignment of groups E – G in class II | ||
---|---|---|---|
Gas and vapor | Dust | ||
Group A | Acetylene | Group E1 | Flammable metal dust, including aluminum, magnesium, or similar substances |
Group B | Flammable gas, flammable vapor, or flammable vapor/air mixtures, including hydrogen, butadiene, ethylene oxide, propylene oxide | Group F | Flammable dust containing carbon, e.g. black coal, carbon dust, charcoal, and coke dust |
Group C | Flammable gas, flammable vapor, or flammable vapor/air mixtures, including ethylene, acetaldehyde, cyclopropane, ether, hydrogen sulfide | Group G | Flammable dust not covered by group E or F, including flour, grain, wood, plastic, and chemicals |
Group D | Flammable gas, flammable vapor, or flammable vapor/air mixtures, including propane, acetone, alcohol, ammonia, gasoline, solvents, natural gas, propylene | - | – |
|
We have stored a table for you here.
The table is not complete. For a full description of the groups, refer to the standards NEC 500.6 (A) and (B) and C22.1.
Temperature classes
EDR.., EDRN.. motors in class I and class II for hazardous locations are additionally labeled with the respective temperature class. It is listed on the nameplate and specifies the maximum surface temperature.
The following table shows all possible temperature classes.
Close table
Temperature class | Maximum surface temperature |
---|---|
T1 | 450 °C |
T2 | 300 °C |
T2A | 280 °C |
T2B | 260 °C |
T2C | 230 °C |
T2D | 215 °C |
T31) | 200 °C |
T3A | 180 °C |
T3B1) | 165 °C |
T3C1) | 160 °C |
T4 | 135 °C |
T4A1) | 120 °C |
T5 | 100 °C |
T6 | 85 °C |
|
We have stored a table for you here.
Degree of protection for housings
Just as the degree of protection for housings is specified according to IEC 60529, the NEMA (National Electrical Manufacturers Association) Standard Publication No. 250, among others, applies in the USA. This describes the degree of protection for housings. The degrees of protection cannot be compared directly to the IEC degrees of protection.
The requirements of motors for the USA are defined according to NEMA MG 1, or ANSI/IEC 60529. In Canada the requirements are defined according to CSA 22.2 no. 60529
The EDRN.. motors comply with NEMA TEFC (totally enclosed, fan-cooled) and IEC degree of protection IP55.
Identification
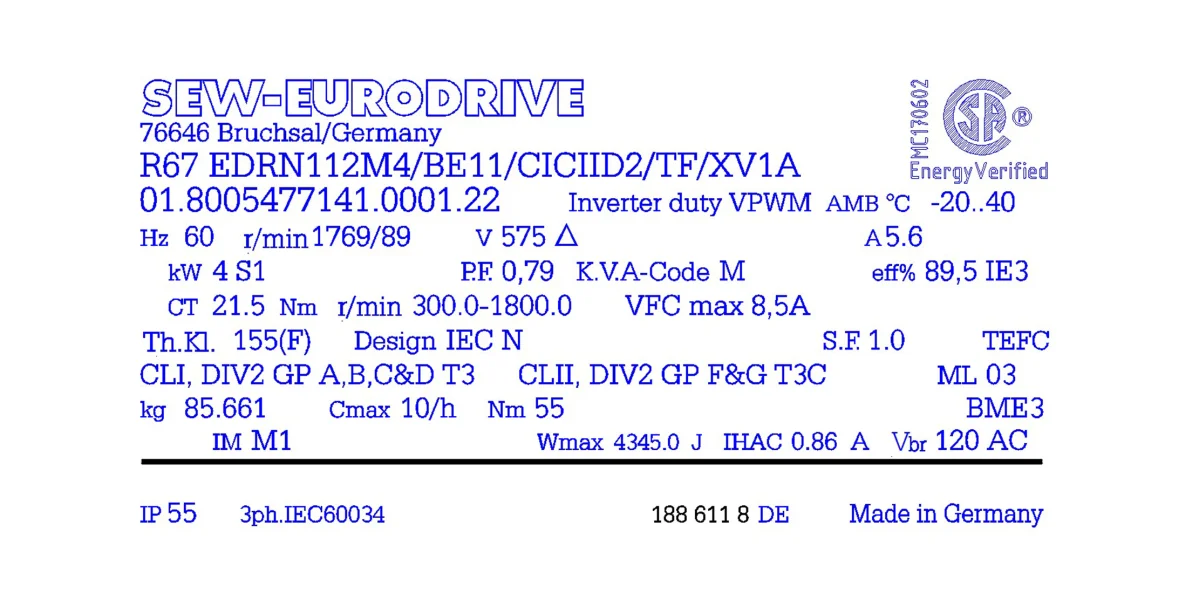
In addition to data such as manufacturer, type, serial number and electrical data, data relevant for explosion protection must be included in the identification of the operating resources. The relevant specifications can be found in the NEC, the CEC and the corresponding design specifications of the inspection authorities.
Approved electric operating resources for class I, class II and class III, division 1 and division 2 should be marked with the following information:
- Class(es), division(s) (optional except for division 2)
- Gas/dust group(s)
- Operating temperature or temperature class (optional for T5 and T6)
Example: Class I Division 2 Groups C D T4
Operation of motors on a frequency inverter
Increasingly variable speeds are required in areas with potentially explosive atmospheres. As such, motors with explosion protection must be suitable for operation on a frequency inverter.
Here, too, protection from impermissible heating and avoidance of sparking is of the utmost priority.
The EN IEC 60079-0, EN IEC 60079-7, EN 60079-31 and EN 60079-14 standards provide information regarding the operation of motors that are operated with an inverter.
An inverter is also known, for example, as a frequency inverter, converter drive, DC-AC inverter, adjustable-speed drive (ASD), drive with adjustable speed, or variable frequency drive (VFD).
-
Permitted operating modes and protection concepts for motors
-
Safe operation of motors in category 2 and 3
-
Safe operation of category 3 motors – group drive
The equipment categories, protection levels, and protection types must be taken into account during configuration and selection. The following describes the special features for motors of the protection types Ex eb, Ex ec as well as Ex tb and Ex tc.
Close table
Design | Operating modes on nameplate | Additional nameplate | Permitted operating modes | Protection against excessive heating | Identification on the nameplate |
---|---|---|---|---|---|
2G, 2D, 2GD 2G-b 2D-b 2GD-b |
S1 | VFC | Inverter operation | PTC thermistor/TF1 and speed-dependent current limiting in the inverter2. | Additional nameplate: X identification and permitted continuous currents are indicated depending on the frequency |
3G, 3D, 3GD 3G-c 3D-c 3GD-c |
S1 | VFC VFCe |
Inverter operation, group drive (only 3D) | PTC thermistor/TF1 | Additional nameplate: Permitted continuous currents listed depending on the frequency |
|
We have stored a table for you here.
Motor operation on the frequency inverter – these points are considered
If a motor is operated on the frequency inverter, these points will be factored into the selection and startup process:
- Max. nominal voltage of the motor
- Permitted voltage stress of the motor
- Thermal limit characteristic curve of the motor
- Nominal continuous currents of the motor and inverter
- Brief overload of the motor and inverter
- Current monitoring setting in the inverter
- The limit speed frequency, minimum frequency, and maximum frequency must be monitored by the inverter.
- The overload time is based on a 10 min. time interval.
- The minimum clock frequency of 3 kHz must be maintained.
-
Maximum nominal voltage
-
Voltage stress in inverter operation
-
Thermal limit characteristic curves for inverter operation
-
Typical application
-
Special application
-
Operating mode for frequency inverter
The maximum permitted nominal EDR.. motor voltage for inverter operation is 500 V.
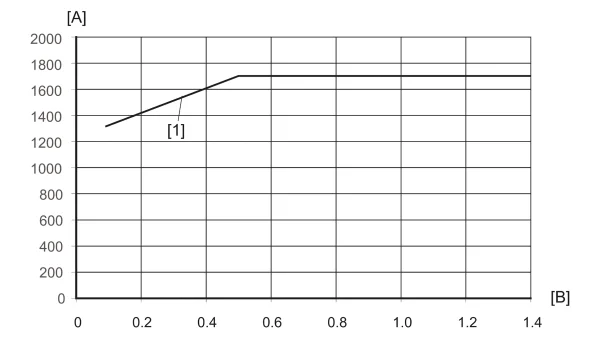
When asynchronous motors are operated at an inverter, the winding is subject to higher loads than would be the case in line operation without inverter. An inverter pulses the DC voltage of the DC link (Vz) to the supply cables to the motor. This pulsed voltage supply takes place in the kHz range, which means several thousand ON and OFF switchings per second – at SEW-EURODRIVE usually with 4, 8, 12 or 16 kHz.
Operating motors from SEW‑EURODRIVE on inverters is permitted if the pulse voltages at the motor terminals indicated in the following figure are not exceeded:
[A] Permitted pulse voltage ULL in V (ULL = voltage between two outer conductors)
[B] Rise time in µs
[1] Permitted pulse voltage for EDR../EDRN.. motors
Maintaining voltage limit values
The following limit values must be verified and adhered to:
- The supply voltage level
- The threshold of the brake chopper voltage
- The operating mode of the motor (motor mode/generator mode)
If the permitted pulse voltage is exceeded, you must install limiting measures, such as filters, chokes or special motor cables.
Frequency inverters from SEW-EURODRIVE
When using frequency inverters from SEW‑EURODRIVE at line voltages of up to 500 V and in non-regenerative operation, the maximum permitted limit values of the motors are met. The pulse voltage at the motor terminals (caused by reflections) depends, among others, on the level of the DC link voltage and the cable length between frequency inverter and motor.
If regenerative operation cannot be ruled out, a braking resistor must be configured and connected to the frequency inverter to avoid an increased DC link voltage.
If EDRN.. motors are operated with inverter, the thermally permitted torque must be observed during drive project planning. The thermally permitted torque depends on the following factors:
- Motor size
- Type of cooling – Self-cooling or forced cooling fan
- Base frequency: fEck = 50 Hz (400 V star connection) or fEck = 87 Hz (230 V delta connection)
- Motor terminal voltage
The effective operating point resulting from the travel cycle must lie below the limit curve. It consists of the effective torque and the mean rotational speed.
Points A to E describe the motor torque curve in the ideal case where the motor terminal voltage corresponds to the rated motor voltage. Points A, B and C define the "reduced" torque in the lower speed range caused by the reduced motor cooling. These values are independent of the voltage. Points D to E describe the curve of the torque characteristic in the field weakening. Field weakening begins at point D. Point E is the permitted thermal torque at limit speed. Both points depend on the voltage and must be calculated when configuring the motor.
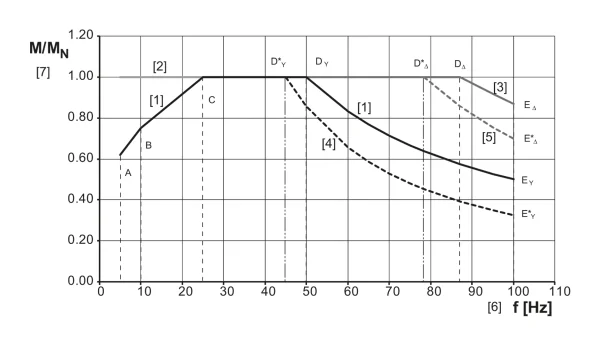
The ideal case described above does not occur in reality because drive components such as inverters, filters, and cables are subject to voltage losses. To avoid having to configure the voltage-dependent part of the characteristic curve (points D and E) for each motor, the "typical application" is defined for explosion-protected motors according to ATEX and IECEx.
The left diagram shows the typical limit characteristic curve for EDRN63 – 225 motors.
[1] Star connection
[2] Forced cooling fan
[3] Delta connection
[4] Typical application – star connection
[5] Typical application – delta connection
[6] Operating frequency of the motor
[7] Torque ratio M/MN
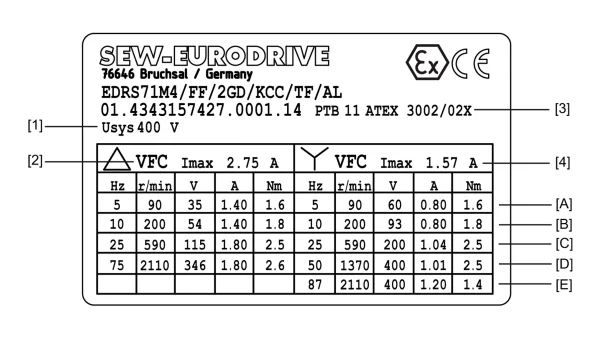
The exact values can be found in the documentation and on the additional nameplate for frequency inverter operation
[1] System voltage – line voltage of the frequency inverter
[2] (Voltage Mode Flux Control) Voltage‑controlled control mode of the frequency inverter and connection type
[3] EU type examination certificate for frequency inverter operation
[4] Maximum permitted peak current, e.g. when accelerating with VFC control mode
[A] [B] [C] [D] [E]
The additional FI nameplate lists the thermal limit characteristic curve of the motor (point A – E) considering voltage and frequency.
The minimum and maximum frequency can differ depending on the option.
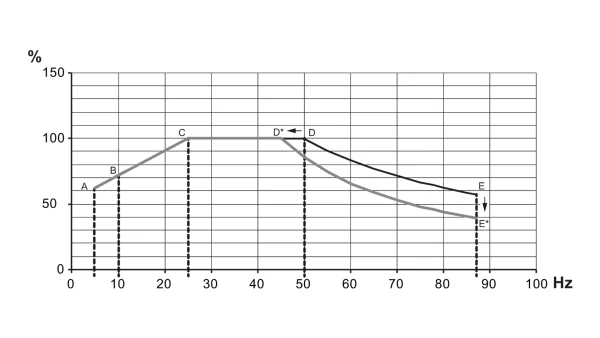
The typical application is distinguished by the fact that not all of the supply voltage is available at the motor terminal board due to the voltage drop in the inverter and in the motor cable. This means that points D and E shift and the new points D* and E* result in a new field weakening curve.
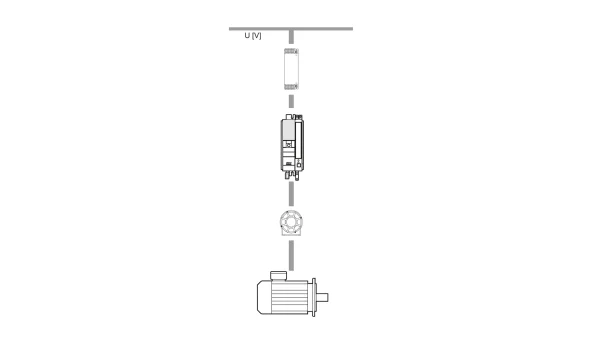
The typical application is defined by the following conditions:
- Rated motor voltage = line voltage
- E.g. rated motor voltage1) 230/400 V at a line voltage of 400 V
- Line voltage tolerance ≤ 5%
- Motor line length ≤ 100 m and motor line voltage drop ≤ 10 V
- Use of the MOVITRAC® B or MOVIDRIVE® inverter series
- No line chokes or sine filters are used
- Installation of HD output choke
- Installation with and without external NF line filter
1) Choose the rated motor voltage depending on the line voltage.
If all conditions are met, a motor terminal voltage of at least 360 V is ensured. If one of these conditions is not met, you must calculate the motor terminal voltage. You can find related information under the "Special application" tab.
If the conditions of the typical application are not met, the motor terminal voltage can deviate and, as a result, the motor can heat up excessively.
The deviating motor terminal voltage changes the shape of the thermal characteristic curve. The calculation and observation of points D (field weakening fD) and E (current limit IE and torque ME) during startup prevents the motor from overheating.
You have to calculate the current limit IE only for drives of category 2.
The project planning procedure is as follows:
- Calculate the motor terminal voltage
- Calculate the field weakening fD*
- Calculate the torque characteristic ME*
- Calculate the current limit IE* for category 2 motors
During operation on the frequency inverter, the setting range and therefore the minimum frequency/speed and overload behavior/dynamics in particular are an important factor in fulfilling the application’s requirements.
Low speeds and compliance with the permissible limit values such as the permissible motor current therefore also necessitate requirements for the inverter’s control mode.
In the case of asynchronous motors, nearly all inverters today have a voltage-controlled, field-oriented control mode. Therefore, all the certificates include operating motors on voltage-controlled frequency inverters.
SEW-EURODRIVE offers EDRN.. motors with various operating data.
Operation on a frequency inverter with VFC operating data
Operation on a frequency inverter with VFCe operating data
On motors with VFC (Voltage Flux Control) operating data, you can operate the motors with a minimum frequency of 5 Hz and a brief maximum current of 150% of the nominal motor current (approx. 150% of the nominal torque).
Motors are available in category 2 and 3, or EPL b and c, each in gas and dust.
Voltage-controlled frequency inverters (U/f, vector-oriented, e.g. SEW-EURODRIVE frequency inverters with VFC or VFCPLUS control mode) are approved.
On motors with VFCe (VFCe = Voltage Flux Control extended) operating data, you can operate the motors with a minimum frequency of 0.3 Hz and a brief maximum torque of 160% to 380% of the nominal motor torque. It is necessary to have a speed sensor and a voltage-controlled frequency inverter that possesses a field-oriented control mode. In this case, the ideal combination is the high-resolution sine/cosine encoder, e.g. EK8S, and a MOVIDRIVE®application inverter from our MOVI‑C® modular automation system.
Motors are available in category 3 or EPL c, each in gas and dust.
Voltage-controlled frequency inverters (vector-oriented, … e.g. SEW‑EURODRIVE frequency inverters with VFC or VFCPLUS control mode) are approved.
The operating mode and the operating data are shown on the additional nameplate for frequency inverter operation.
Project planning is the basic requirement for safe operation of explosion-protected motors.
The following points have to be considered:
- Checking the conditions of the typical application
- In the event of deviations from the typical application: Calculate the motor terminal voltage
- Adhere to the thermal torque limit characteristic curve
- Observe the dynamic limit torque
- Observe motor limit frequency
- Select the suitable frequency inverter
- Use a braking resistor if regenerative operation cannot be ruled out.
- Check the overhung and axial loads on the motor shaft of stand-alone motors.
- Observe the maximum gear unit input speed, see Memax on the nameplate.
- Observe the maximum gear unit output torque, see Mamax on the nameplate.
- The maximum permitted braking work per emergency stop must be observed.
Close table
General | Category 2 and 3 | |
---|---|---|
Install the frequency inverter outside the potentially explosive atmosphere. | ||
Motor terminal voltage | Category 2 and 3 | |
The calculation of the motor terminal voltage is an important component of project planning. If the conditions differ from the typical application, you have to calculate the start of field weakening fD* and the torque ME*. |
||
Maximum permitted torques | Category 2 and 3 | |
The thermal torque limit characteristic curve shows the permitted maximum torque for continuous operation of the motor. If the effective operating point is below the thermal limit characteristic curve, the values may be exceeded briefly. |
||
Category 2 | ||
The permitted maximum dynamic limit torque is determined by the short-term current limiting (150% IN motor). For the value IN motor, refer to the EU type examination certificate or the nameplate. |
||
Permitted maximum and minimum frequencies | Category 2 and 3 | |
The maximum and minimum frequencies are indicated on the nameplate. The actual values may not exceed or fall below these specifications. | ||
Thermal motor protection | Category 2 and 3 | |
Only motors that are equipped with a PTC thermistor (option /TF) are permitted for operation on an inverter to ensure that the permitted limit temperature is not exceeded. This must be evaluated using an appropriate device. | ||
EMC measures | Category 2 and 3 | |
The following components are permitted for the inverters of the MOVIDRIVE® and MOVITRAC® series:
|
We have stored a table for you here.
Group drive means that several motors are operated simultaneously on one inverter. Only EDR../EDRN.. motors of category 3D may be operated in group drive.
Motors in 3D design may be used as group drives in zone 22 if each individual motor of the group has been configured, designed, and identified for inverter operation.
The following restrictions apply:
- For applications, the individual motors must be connected slip-free, non-positive, or positive.
- Only identical motors may be used, which means motors with the same rated data (power, speed, voltage, and frequency).
- Nominal output current of inverter ≤ 1.5 × sum of nominal motor currents.
- Each motor must be designed with a thermal motor protection (PTC thermistor).
- Each individual temperature sensor must be externally monitored by a separate evaluation unit.
- If an evaluation unit trips, all motors of the group must be stopped.
Explosion-protection abbreviations
-
Explanations
Close table
ANSI | American National Standards Institute |
---|---|
ATEX | Atmosphere Explosible |
CCCEx | China Compulsory Certification for Ex equipment |
CCoE | Chief Controller of Explosives |
CoC | Certificate of Conformity |
CSA | Canadian Standards Association |
DNV | Det Norske Veritas, today DNV GL |
EU | European Union |
EPL | Equipment protection level |
ExCB | Ex-Certification Bodies |
ExTL | Ex-Testing Laboratory |
HazLoc-NA® | Hazardous Location North America – Synonym for explosion protection in USA and Canada |
IECEx | International Electrical Committee – Explosion protection system |
INMETRO | Brazilian Federal Institute for Metrology |
KCs | Korean Certified safety |
KOSHA |
Korea Occupational Safety and Health Agency |
MEPS | Minimum Efficiency Performance Standard |
NEPSI | National Supervision and Inspection Center for Explosion Protection and Safety of Instrumentation |
NFPA | National Fire Protection Association |
PESO | Petroleum and Explosives Safety Organization |
PTB | Physikalisch-Technische Bundesanstalt |
UA.TR | Ukrainian Technical Regulations |
UKCA | UK Conformity Assessed |
We have stored a table for you here.
We're happy to help.
Do you have more questions about SEW-EURODRIVE or need some advice from us? Just send us a message with your questions.
Contact us now